The year 2005 was marked by a flurry of
construction activity in the Nation’s ethanol industry, as ground was
broken on dozens of new plants throughout the U.S. Corn Belt and plans
were drawn for even more facilities. As of February 2006, the annual
capacity of the U.S. ethanol sector stood at 4.4 billion gallons, and
plants under construction or expansion are likely to add another 2.1
billion gallons to this number (map). If this trend and the existing and
anticipated policy incentives in support of ethanol continue, U.S.
ethanol production could reach 7 billion gallons in 2010, 3.3 billion
more than the amount produced in 2005.
The
tremendous expansion of the ethanol sector raises a key question: Where
will ethanol producers get the corn needed to increase their output?
With a corn-to-ethanol conversion rate of 2.7 gallons per bushel (a rate
that many state-of-the-art facilities are already surpassing), the U.S.
ethanol sector will need 2.6 billion bushels per year by 2010—1.2
billion bushels more than it consumed in 2005. That’s a lot of corn, and
how the market adapts to this increased demand is likely to be one of
the major developments of the early 21st century in U.S. agriculture.
The most recent USDA Baseline Projections suggest that much of the
additional corn needed for ethanol production will be diverted from
exports. However, if the United States successfully develops cellulosic
biomass (wood fibers and crop residue) as an economical alternative
feedstock for ethanol production, corn would become one of many crops
and plant-based materials used to produce ethanol.
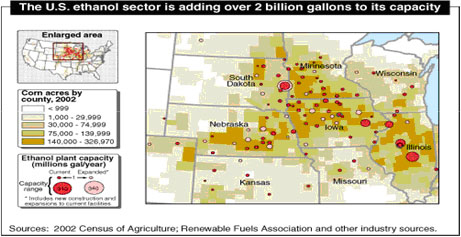
#That
70s Energy Scene
The factors behind ethanol’s resurgence
are eerily reminiscent of the 1970s and early 1980s, when interest in
ethanol rebounded after a long period of dormancy. First, the price of
crude oil has risen to its highest real level in over 20 years,
averaging more than $50 per barrel in 2005. Long-term projections from
the U.S. Department of Energy’s Energy Information Administration (EIA)
suggest that the price of imported low-sulfur light crude oil will
exceed $46 per barrel (in 2004 prices) throughout the period 2006-30 and
will approach $57 per barrel toward the end of this period. It is
important to remember, however, that as the price of oil dropped during
the first half of the 1980s, so, too, did ethanol’s profitability.
Second, many refineries are replacing
methyl tertiary butyl ether (MTBE) with ethanol as an ingredient in
gasoline. Oxygenates such as MTBE and ethanol help gasoline to burn more
thoroughly, thereby reducing tailpipe emissions, and were mandated in
several areas to meet clean air requirements. But many State governments
have recently banned or restricted the use of MTBE after the chemical
was detected in ground and surface water at numerous sites across the
country. In the 1970s and 1980s, a similar phaseout ended the use of
lead as a gasoline additive in the United States. Both ethanol and lead
raise the octane level of gasoline, so the lead phaseout also fostered
greater use of ethanol.
Third, the
Energy Policy Act of 2005 specifies a new Renewable Fuel Standard (RFS)
that will ensure that gasoline marketed in the United States contains a
specific minimum amount of renewable fuel. Between 2006 and 2012, the
RFS is slated to rise from 4.0 to 7.5 billion gallons per year.
Assessments of the existing and likely future capacity of the U.S.
ethanol industry indicate that the RFS will easily be achieved. The RFS
joins a long list of incentives that the State and Federal governments
have directed toward ethanol since the 1970s. One of the most important
of these incentives is the Federal tax credit, initiated in 1978, to
refiners and marketers of gasoline containing ethanol. The credit, which
may be applied either to the Federal sales tax on the fuel or to the
corporate income tax of the refiner or marketer, currently equals 51
cents per gallon of ethanol used.
Where Will the Corn Come From?
Large corn stocks will enable U.S.
ethanol production to increase initially without requiring much
additional adjustment in the corn market. The U.S. ended the 2004/05
marketing year (MY—September 2004-August 2005) with stocks of 2.1
billion bushels—enough to produce 5.7 billion gallons of ethanol. As
long as corn is the primary feedstock for ethanol in the U.S., however,
sustained increases in ethanol production will eventually require
adjustments in the corn market.
One possibility is that ethanol producers
will secure the additional corn they need by competing with other buyers
in the marketplace and bidding up the price of corn. According to the
USDA Agricultural Baseline Projections (released in February 2006), the
share of ethanol in total corn use will rise from 12 percent in 2004/05
to 23 percent in 2014/15. A comparison of the 2006 Baseline with the
2005 Baseline suggests that much of the increased use by ethanol
producers will be diverted from potential exports; the 2006 Baseline
projects higher use for ethanol and lower exports than the 2005
Baseline.
If demand for ethanol reduces the
availability of U.S. corn for export, one might ask how this will alter
the geographical composition of U.S. exports. The 2006 Baseline suggests
that among the major foreign buyers of U.S. corn, Japan and Taiwan are
likely to be the least responsive to a rise in corn prices, while
Canada, Egypt, and the Central American and Caribbean region are likely
to be the most responsive. Japan and Taiwan both have relatively high
per capita incomes and limited corn production. In contrast, Canada,
another high-income country, has substantial levels of corn production
and could respond to higher prices with increased output of corn, wheat,
and other feed grains. Per capita income in Egypt, Central America, and
the Caribbean is relatively low, and higher prices may drive these
countries to cut back in corn use, increase domestic corn production, or
seek out substitutes. Egypt already produces a sizable amount of corn.
Slower growth of U.S. corn exports would
create new opportunities for corn producers in other parts of the world,
including Argentina, Brazil, and China. Another country to watch is
Mexico, where irrigated lands have accounted for about half of the
increase in domestic corn production since the late 1980s. Much of this
increase has taken place in the State of Sinaloa, where farmers are
applying advanced agricultural techniques to obtain yields comparable to
those in the United States. Sinaloa, however, is relatively distant from
corn-deficit areas in Mexico, and many of these producers have counted
on marketing subsidies to offset some of the transportation costs.
Increased demand for corn by U.S. ethanol producers might push prices
high enough that these transportation costs are more easily surmounted.
Farmers May Increase Corn Supply
The growing corn demand of ethanol
producers could also be satisfied through higher corn output. Rising
productivity is likely to assure some increase in U.S. corn production
in the years to come, even if the amount of farmland devoted to corn
remains constant. Over the past decade (1996-2005), U.S. corn yields
averaged 138 bushels per acre, compared with 115 bushels during the
previous decade. The United States also could increase corn production
by devoting more land to the commodity. Such an effort would probably
draw upon lands less suited to corn production. Much of these lands
would probably be diverted from soybean production.
Growing corn more intensively is yet
another approach. For instance, some producers who currently pursue a
corn-soybean rotation (planting corn one year and soybeans the next)
might shift to a corn-corn-soybean rotation (planting corn 2 years in a
row and then planting soybeans in the third). Continuous production of
corn (planting corn every year on the same plot of land) is another
possibility. Interestingly, one of the key factors boosting ethanol
demand—high oil prices—also makes intensive corn production less
attractive because more fertilizer would be needed.
One way to get more ethanol feedstock out
of existing levels of corn production is to use the stalk, leaves, and
cobs left over after harvest—materials that are formally known as
stover. An acre of corn will yield roughly 5,500 dry pounds of stover,
enough to produce about 180 gallons of ethanol. In the United States,
corn stover is typically left in the field following harvest to minimize
erosion and to contribute organic matter to the soil, so removing some
of the stover at harvest might adversely affect the long-term viability
of the soil.
Market Adjustments Extend to Ethanol
Co-Products and Beyond
As ethanol production increases, the
supply of ethanol co-products will also increase. Both the dry-milling
and wet-milling methods of producing ethanol generate a variety of
economically valuable co-products, the most prominent of which is
perhaps distiller’s dried grains with solubles (DDGS), which can be used
as a feed ingredient for livestock. Each 56-pound bushel of corn used in
dry mill ethanol production generates about 17.4 pounds of DDGS. In the
United States, cattle (both dairy and beef) have so far been the primary
users of DDGS as livestock feed, but larger quantities of DDGS are
making their way into the feed rations of hogs and poultry. Use of
distiller’s grains in animal production lowers the use of corn and
protein supplements.
The marketing of ethanol co-products is
just one way in which ethanol producers are making their operations more
profitable. Another way is to save energy by locating ethanol plants in
close proximity to dairy or livestock production. Specifically, a dairy
or livestock producer is able to lower the transport costs associated
with feed acquisition by establishing a nearby facility to manufacture
ethanol and distiller’s grains. The latter may be quickly transported to
feed nearby livestock without needing to be dried, and the manure
generated by the livestock can be used to produce heat or electricity
for the ethanol plant, but this entails a sizable capital cost.
Closer integration of ethanol production
with other agri-industrial activities is likely to displace some
traditional marketing and distribution channels for corn. Indeed, the
services of some grain elevators may no longer be needed in some areas
if local corn supplies are used in their entirety for ethanol
production. The transportation sector may be the site of several
noteworthy adjustments, as the profitability of the expanded ethanol
sector will depend on economical methods of handling the growing supply
of ethanol and its co-products, as well as the feedstock necessary to
produce them. Some large-scale ethanol plants may find it cost effective
to receive corn deliveries by rail on specially constructed trunk lines,
while others may rely on truck, barge, or existing rail lines, depending
on the location of the facility. The transportation of ethanol requires
special attention. Ethanol is usually not moved across large distances
by pipeline because the product has the ability to absorb the water and
impurities commonly found in pipelines. Instead, the product is
customarily shipped in tanks by train, truck, or barge, and then mixed
directly with gasoline in the tanker trucks that deliver fuel to gas
stations.
New Feedstocks Are the Wild Card
The search for ethanol feedstocks will
not stop at the edge of the corn field. While corn is currently the
primary feedstock for U.S. ethanol production, many other agricultural
commodities and plant-generated materials can be used to produce the
fuel. For example, ethanol derived from sugar cane satisfies roughly
half of Brazil’s annual demand for motor vehicle fuel, and sorghum is
the feedstock for about 3 percent of U.S. ethanol production.
The U.S. and many other countries are
very interested in cellulosic biomass as a potential feedstock for
ethanol. Cellulosic biomass refers to a wide variety of plentiful
materials obtained from plants—including certain forest-related
resources (mill residues, precommercial thinnings, slash, and brush),
many types of solid wood waste materials, and certain agricultural
wastes (including corn stover)—as well as plants that are specifically
grown as fuel for generating electricity. A report prepared for the U.S.
Department of Energy and USDA in 2005 suggests that, by the middle of
the 21st century, the United States should be able to produce 1.3
billion dry tons of biomass feedstock per year—enough to displace at
least 30 percent of its current petroleum consumption.
Harnessing cellulosic biomass to produce
ethanol will require the development of economically viable technologies
that can break the cellulose into the sugars that are distilled to
produce ethanol. No one knows for sure how long it will take to develop
these technologies, although the more optimistic predictions are in the
neighborhood of 5-10 years. To expedite the achievement of this goal,
the Energy Policy Act of 2005 directs incentives specifically toward the
use of cellulosic biomass as a feedstock for renewable fuel. For the
purpose of meeting the Renewable Fuel Standard, 1 gallon of cellulosic
biomass ethanol is treated as 2.5 gallons of renewable fuel through the
end of 2012. The Act also provides for research, development, and
demonstration projects concerning cellulosic biomass, and it mandates
that at least 250 million gallons of renewable fuel be produced per year
using cellulosic biomass, beginning in 2013. Until cellulosic biomass is
successfully commercialized, however, corn will almost certainly remain
the primary feedstock for U.S. ethanol production.
Ethanol Futures
Information
Ethanol Futures
Contract Size
29,000 U.S. gallons
(approximately one rail car)
Deliverable
Grades for an Ethanol
Futures Contract
Denatured Fuel
Ethanol as specified in The American Society for Testing and Materials
standard D4806 for Denatured Fuel Ethanol for Blending with Gasolines
for Use as Automotive Spark-Ignition Engine Fuel plus California
standards.
Tick Size
One tenth of one
cent ($0.001) per gallon ($29 per contract)
Price Quote
Dollars and
cents/gallon
Ethanol Futures
Contract Months
All calendar months
Ethanol Futures
Last Trading Day
The 3rd business day
of the delivery month.
Last Delivery Day
for Ethanol Futures
The second business
day following the last trading day of the delivery month.
Ethanol Futures
Trading Hours
Open Auction: 9:30
a.m. - 1:15 p.m. Chicago Time
Electronic Platform: 6:36 p.m. - 6:00 a.m. and 9:30 a.m. to 1:15 p.m.
Chicago Time
Note: Expiring contract closes at 12:00 noon on Last Trading Day.
Ethanol Futures
Ticker Symbols
AC for Open Auction
ZE for Electronic
Ethanol Futures
Daily Price Limit
Thirty cents ($0.30)
per gallon ($8,700 per contract) above or below the previous day's
settlement price. No limit in the spot month ( limits are lifted
beginning on First Position Day
|